
Fourier transform-infrared spectroscopy, contact angle, and water suspension of AF suggest that plasma treatment using ethylene successfully modifies the surface nature of AF from hydrophilic to hydrophobic. The role of the AF content (3, 6, 9, 12, and 15 wt.%) and its surface modification on the cellular morphology and mechanical properties of LDPE/EVA/AF foams under compression is investigated herein. The above results suggest that the plasticized UHMWPE improves interfacial chains diffusion and acts as a nucleating agent to enhance the foamability of HDPE/p-UHMWPE blends.Īgave fibers (AF) were incorporated either pristine (AFp) or surface treated by ethylene plasma (AFm) in low-density polyethylene (LDPE)/ethylene vinyl acetate (EVA) blends at a ratio of 1 : 1 and foamed by chemical means.
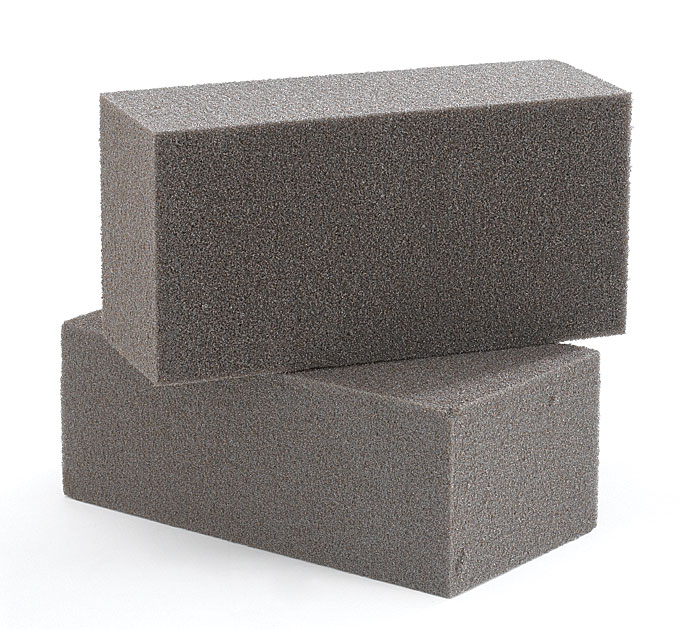
After batch foaming of the plasticized UHMWPE containing blends, optimum cell size and density, volume expansion ratio (VER), compressive strength, and improved crystalline characteristics are observed for the blend containing 20 wt.% plasticized UHMWPE. Further, blends of plasticized UHMWPE reflect a reduction in microcracks and fibrillated microstructures with a switch over to corrugated and island in-the-sea morphology from scanning electron microscopy (SEM) images. In addition, blends containing plasticized UHMWPE reveal immiscibility by improving shear-thinning behaviour as well as melt elasticity during the small amplitude oscillatory shear (SAOS) based frequency sweep tests. Interestingly, the slit capillary rheology data on application of the power-law model establish the rheological percolation threshold to be at 20 wt.% of plasticized UHMWPE content. The tensile strength of ~ 3–14%, Young’s modulus of ~ 33–36% and impact strength of ~ 77–175% of blends improve with plasticized UHMWPE content. The reduction in the percentage crystallinity with neat UHMWPE loading without affecting thermal transition temperatures indicates immiscibility of components.
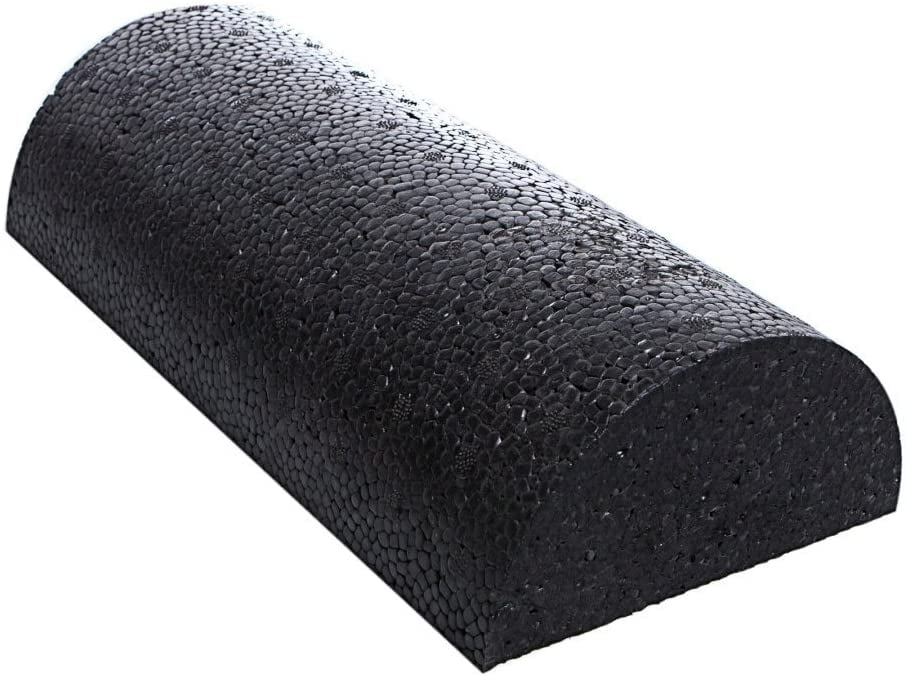
Fischer–Tropsch (H5) olefin wax is added to prepare plasticized UHMWPE (p-UHMWPE) and incorporation of plasticized UHMWPE reduces the processing time for melt blending.

The extent to which plasticization of ultrahigh molecular weight (UHMWPE) can modify the micro- as well as macro-structural properties of HDPE/UHMWPE blends as well as their foam characteristics are investigated in the present study by preparing blends using melt mixing and further foaming of the developed blends using supercritical CO2 (scCO2). It was also possible to produce geopolymer formulations that could be printed using additive manufacturing technology (Direct Ink writing), which enabled to produce components with nonstochastic porosity. The foams, due to their low thermal conductivity, could also be used for thermal insulation. The foamed geopolymer can also be used as adsorbents for the removal of copper and ammonium ions from wastewater. The results showed that the cell size and size distribution can be controlled by adding different content of surfactant and foaming agent. Moreover, factors that influence the compressive strength, the porosity, the thermal conductivity, and the cell size distribution were investigated.

Slurries processed in optimized conditions enabled to fabricate potassium based GFs with a total porosity in the range of ∼67 to ∼86 vol% (∼62 to ∼84 vol% open), thermal conductivity from ∼0.289 to ∼0.091 W/mK, and possessing a compressive strength from ∼0.3 to ∼9.4 MPa. High-porosity metakaolin-based geopolymer foams (GFs) were fabricated by a gelcasting technique using hydrogen peroxide (foaming agent) in combination with Tween 80 (surfactant).
